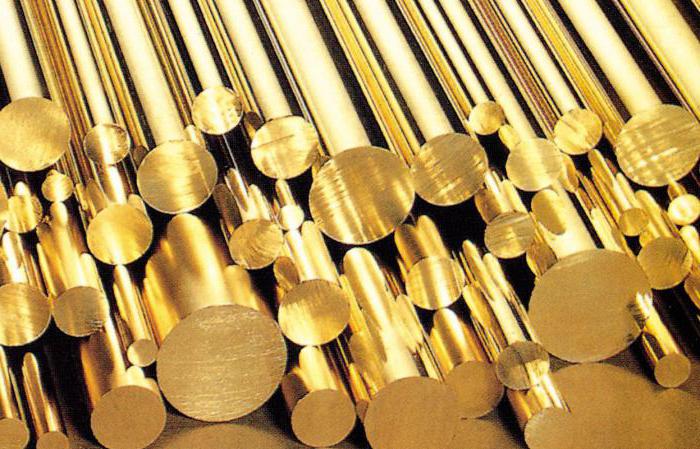
There is a wide variety of metals and alloys in the commercial field, copper and brass being two metals that are often confused. In this article, we aim to introduce you to the copper and brass alloys, which are widely used in the industry for CNC machining, with their most distinctive features.
Copper
Copper, which has been actively used since ancient times in human history, is a pure metal suitable for direct processing. Copper, which is antimicrobial in nature, is very soft in its purest form and can be easily hammered. In addition, it offers high electrical and thermal conductivity as well as high corrosion resistance. The electrical and electronics industry frequently benefits from these properties of copper.
Copper is one of the cost-effective CNC machining metals with its very high machinability rate. With excellent thermal and electrical conductivity, C101 and C110 copper alloys are widely used for CNC machining.
C101, also known as “oxygen-free copper”, is an extremely high purity alloy with a Cu content of 99.99% and shows excellent electrical conductivity and is therefore also called “HC (high conductivity)” copper. In addition, C101, which has good strength values and high ductility, is an indispensable alloy in the electrical-electronics industry. With its effective corrosion resistance, it is used in various engineering applications such as cables, motor components and transformers.
C110, also known as “electrolytic hard pitch (ETP)”, although not as pure as the C101 alloy with its 99.9% Cu content, is a very pure alloy and shows high electrical conductivity. It is more cost-effective and easier to process than the C101 alloy. In addition, C110 alloy can be easily formed by cold forming methods. C110 alloy is also frequently preferred for electrical-electronic applications.
Brass
Brass, a metal alloy consisting of a combination of copper and zinc, is among the preferred CNC machining metals thanks to its high machinability, although its raw material cost is relatively high. In addition, the high scrap yield brass offsets the raw material cost. Brass is widely known for its medium hardness and high tensile strength. Particularly, zinc concentration improves the strength and ductility values of brass and provides flexibility as well as strength to the alloy. The color of rice changes from red to yellow with increasing zinc concentration.
C260 and C360 alloys with high zinc concentration are often preferred in CNC machining. These alloys have a gold appearance and exhibit superior mechanical properties. They show good corrosion resistance and are highly machinable alloys. They are also ideal for applications requiring low friction.
C260, also known as “yellow brass” or “cartridge brass”, is among the most preferred and cost-effective brass alloys. The most ductile yellow brass, C260 offers good mechanical properties along with superior corrosion resistance. C260 alloy, which has non-hard machinability, can also be cold formed. It is widely used in ammunition components, hinges, fasteners and radiator equipment.
C360, also known as “free machining brass”, has excellent machinability, as its name suggests, thanks to its high lead content. Known as a soft and ductile alloy, C360 brass is also a strong material that exhibits good strength values. Additionally, this alloy has good resistance to corrosion, making it an ideal choice for parts requiring low friction. It is widely used in various machine parts such as nuts, bolts, shafts, bushings, screws and connectors.
Choosing Between Copper and Brass Alloys
Copper offers you excellent electrical and thermal conductivity. With high purity copper alloys C101/HC (99.99% Cu) and C110 (99.9% Cu), you can meet the requirements of your designs that require conductivity while also obtaining the necessary mechanical properties in the parts you produce. In addition, with their high machinability properties, these alloys can be easily processed on CNC machines.
Brass offers you the best machinability of all copper alloys. The copper content in its structure gives brass electrical and thermal conductivity. However, thanks to its zinc content, brass exhibits superior mechanical properties than copper and is a lower-friction material. In summary, brass shows better wear and corrosion resistance than copper. Lead, another alloying element, gives brass excellent machinability.
You can achieve superior mechanical properties and high corrosion resistance in your design with C260, the most ductile yellow brass, and C360, the best machinable alloys. Thanks to their excellent machinability, these alloys can be easily processed on CNC machines, thus saving time and energy. C260 and C360 brass alloys are ideal for fittings that require low friction and high strength.
Copper and brass, known for their electrical conductivity, show significant differences in terms of electrical conductivity values. Superconducting copper, which is considered to be absolutely 100% conductive, is a reference measure by which the electrical conductivity of other materials is evaluated. Brass, which is an alloy of copper and zinc, has an electrical conductivity of approximately 28% of copper.
Conclusion
Choosing materials according to the usage areas of your parts is very important in terms of efficiency and cost in the long run. The alloys of the two metal materials we examined are often used in the production of fasteners with their high machinability and corrosion resistance properties. You can contact us to have your parts produced with copper and brass alloys, which differ from each other with minor differences.