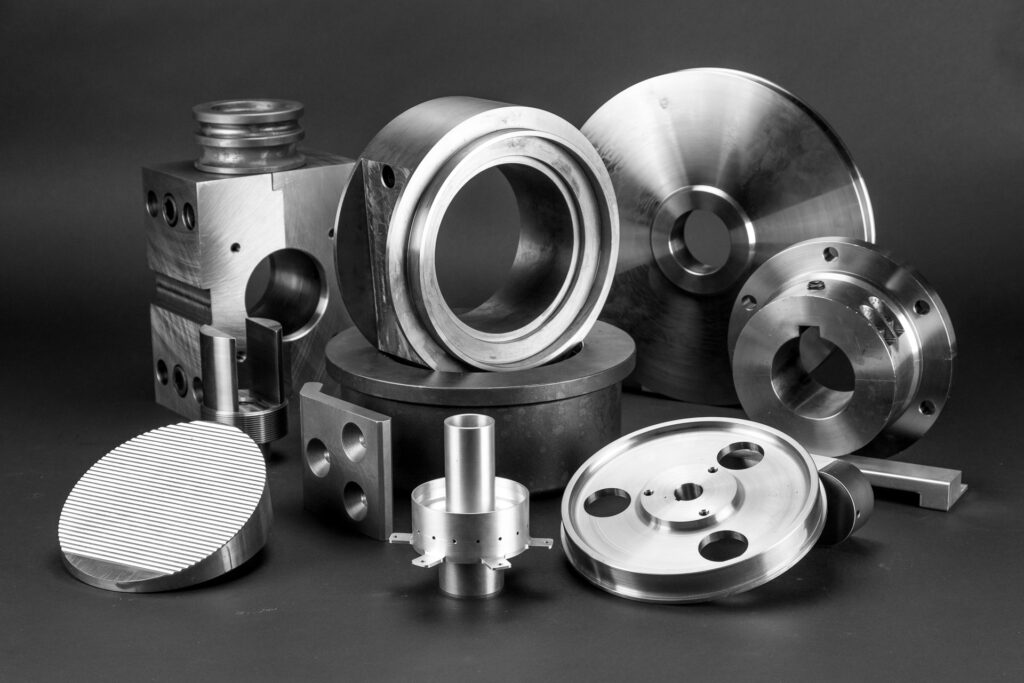
Aluminum is one of the most used materials in CNC machining. Although the most important reason for this is its very good machinability, many features of aluminum play a role in its preference.
Aluminum is one of the most used materials, along with steel, in CNC machining. Although the most important reason for this is its very good machinability, many features of aluminum play a role in its preference.
Aluminum (Al) is a silvery, ductile metal with high oxidation resistance. Its ductility and oxidation resistance make it a widely used material in different industries. Aluminum, which is often used by alloying with different metals to obtain stronger but at the same time light and ductile products, is indispensable especially in the automotive and aerospace industries.
Machinability
Aluminum is a material that can be easily processed on CNC machines thanks to its softness and easy machinability. Its density is about one-third that of steel or copper.
In this way, it ensures that both the workpiece itself and the tool tips are less deformed. This feature provides a significant advantage in terms of time, especially in prototype mold production.
Cost
Aluminum is an element abundant in the earth’s crust. Its abundance in nature makes it very cheap in its raw form. In addition, its easy recycling and 95% energy saving compared to its first production is another factor that facilitates its accessibility. For this purpose, aluminum chips that emerge in CNC machining benches can be reused after being brought together and recycled.
High Strength
As we mentioned before, aluminum is a much lighter metal than steel or copper, with its density of 2.7 g/cm3. Its tensile strength of 49 MPa in its pure form can go up to 700 MPa with different alloys. Despite its lightness, its high strength makes it a widely used material, especially in aviation and automotive.
One of the reasons why aluminum is widely preferred in CNC machining is that it has high corrosion resistance. This feature, resulting from the oxide layer on it, enables it to be frequently used in the shipping industry (in different sea and atmospheric conditions).
Suitability for Anodizing
Anodizing process, which increases the wear and corrosion resistance of metals, is carried out by cleaning the product after production and exposing it to artificial oxidation process. Since aluminum is a metal very suitable for anodizing, its already high corrosion resistance can be further increased.
The 7 Most Used Aluminum Alloys in CNC Machining
In addition to the general properties of aluminum, its alloys also have different properties and their usage areas vary according to these properties. Let’s take a look at the 7 most used alloys of aluminum in CNC machining.
AI-2007 Series
The main alloying element of this series is copper with a ratio of 4-5%. It is a durable, lightweight and highly functional short-chipping alloy. It is also suitable for threading, heat treatment and high-speed machining. In this way, Al-2007 series machine parts are widely used in the production of bolts, rivet nuts, screws and threaded rods. However, this alloy has low weldability and low corrosion resistance. Therefore, it is recommended to carry out protective anodizing after processing.
Al-5083 Series
This series, which is not heat treated, is famous for its excellent resistance to harsh conditions. This alloy, which contains 4-5% magnesium and small amounts of chromium and manganese, is frequently used especially in marine and chemical applications with its high corrosion and wear resistance. It is not recommended for use in applications involving high temperatures.
Al-5754 Series
This alloy, which has a magnesium content of 2.5-3.5%, is the alloy with the highest aluminum content. Al-5754 series is a rollable, wrought and extrudable alloy. Cold processing can be done to increase the strength of this series, which is not heat treated. It has high corrosion resistance and strength like the 5083 series. Considering these properties, it can be understood that 5754 is one of the most popular aluminum alloys used in CNC machining. It is commonly used in welded structures, flooring applications, fishing equipment, vehicle bodies, food processing and rivets.
Al-6060 Series
It is a wrought aluminum alloy containing magnesium and silicon. This heat-treatable alloy has average strength. It is well weldable and formable. It is also highly resistant to corrosion and its resistance can be further increased by anodizing. The 6060 series is commonly used in the construction/architectural, food processing, medical equipment and automotive industries.
Al-6061 Series
It is an alloy containing magnesium, silicon and traces of copper. With its high tensile strength of 180 MPa, it is very suitable for high-load structures such as scaffoldings, railway wagon parts, machinery and aviation parts.
Al-6082 Series
This alloy, produced by rolling and extrusion processes, has medium strength, high weldability and high corrosion resistance. It is frequently used in container parts, ship construction and bridges.
Al-7075 Series
This series, whose main alloying element is zinc, has average machinability and low weldability, but is frequently used in military and aerospace industries, climbing equipment and nuclear applications with its high strength, excellent resistance in atmospheric and marine environments.
Conclusion
Apart from all these, many more aluminum alloys formed with different metals in different proportions are used in CNC machining. With its easy machinability and low cost, it is a metal that you can easily choose both in the prototyping phase and in mass production.